- How To Read Gerber Files
- Export Gerber Files Eagle
- How To Import Gerber Files Into Eagle Pass
- How To Open Gerber Files
- Open Gerber Files In Eagle
How to generate Gerber and Drill files from Eagle 1. Click the CAM Processor button (the one without the green arrow) on the main toolbar. This will bring up the CAM. Click the document icon next to the CAM file name and go to Third Party - Seeed Fusion and select the CAM file. The key here is to click the select button first, pick your gerber file and then once it's selected click import. Let me know if there's anything else I can do for you.
Before you get started, you can upload Eagle .brd
files directly and we’ll generate the gerbers for you. For most users, this is the best way to order a board designed with Eagle.
How To Read Gerber Files
Sometimes though, you might want to customize the silkscreen, manually verify the gerber files, or other things that require manufacturing files. This guide will help with that.
We provide a standard CAM
file that will automatically configure Eagle to a good starting point.
First Steps
Validate Board Outline
One of the most common errors we see for Eagle is a missing Board Outline. Verifying your outline will save you a lot of trouble.
Eagle expects this to be drawn on the Dimension
layer, using the Wire
or Line
tools. For many designs, it’s a simple rectangle or circle that contains your design. We’ll cut your PCB out using this layer as a guide.
Download CAM files
We have published some scripts to automatically download, install, and update our files for Eagle. This is our recommended way to manage your CAM jobs.
Downloading Manually (Manual)
Select the correct CAM file for your version of Eagle, and how many layers you want to use.
For Eagle 7.2 and newer:
For Eagle 7.1, Eagle 6, and Eagle 5:
A good place to save this is in your Eagle folder in the cam/
directory, since Eagle will assume your CAM files are in this folder.
Configuring CAM Output
Load CAM file
To load the downloaded CAM file, open your board layout window. Then, open the CAM processor by going to File
> CAM Processor
Export Gerber Files Eagle
In the new window, select File
> Open Job
, browse to the downloaded file, and select open.
Modify Layer Configuration (Optional)
Once the CAM file is loaded, you may optionally adjust the CAM files to suit your design. The most common adjustment is to add or remove layers that will be included on the silkscreen.
The tabs on top each represent a single Gerber file and a single layer on a fabricated PCB. The list on the right indicates the Eagle layers will be included in this file. It’s common for multiple Eagle layers to be used to generate a single Gerber file.
To adjust the layers used in each file, select the tab (such asTop Silkscreen
), and check or uncheck any layers you would like printed. For a full list of layers and what they typically do, see our Eagle Layers Explained page.
As an example, you can include component values by selecting tValues
, turn off component names by de-selecting tNames
, or show all the Top traces on the top silkscreen by selecting Top
.
How To Import Gerber Files Into Eagle Pass
Note, that while you can configure arbitrary Eagle layers to be included in arbitrary Gerber files, doing so impact the functionality of the board. Silkscreen files are purely cosmetic and safe to change, but excercise caution and verify your gerbers whenever you adjust any other gerber file layer configuration.
Generate the Files
Once the CAM file is loaded and configured to your liking, simply click Process Job
. Eagle will then generate the .ger
and .xln
files in the same folder as your .brd
file.
Eagle will also generate several .gpi
and .dri
files, which can be deleted or ignore.
From here simply zip the output files, and upload it to oshpark.com
Foreword
This post is excellent for those who are looking to extract reference designs (in Gerber files) from silicon manufacturers. In this example, I am trying to save myself from having to draw a PCB trace antenna from scratch! We will copy the reference antenna design from Dialog Semiconductors for its DA14580 BLE chips and use that as a footprint for my PCB.
Let me show you how to extract a component footprint from the Gerber files, |
Tools
Gerber Files
In this example, I downloaded the reference PCB trace antenna design from Dialog (link) and extracted the Gerber files which were in ART format. These are the “blueprints”, if you will, to a PCB manufacturer in terms of how each layer of the PCB is supposed to look like.
PCB Design Software
We will be using Altium Designer 13.1 PCB Design software for this tutorial.
How To Open Gerber Files
Reverse Engineering the Gerber Files
Import Gerber and Drill Files
First, we have to import the Gerber files into Altium Designer. Create a new CAMtastic document by clicking File>New>CAM Document. Next, initiate the import process by clicking File>Import>Gerber.
Select the desired Gerber files (i.e. layers of interest) into the CAMtastic document. |
TIP: Click on “Settings…”. |
TIP: Follow the above settings. |
It is important that you follow the recommended settings during the import. This will guarantee that the dimensions are correct (in my first few attempts, they were several times larger). Now click “OK” to execute the import.
The imported Gerber files. Highlighted here is just the Top layer which I am interested in. |
The import process is not complete yet without the Drill file(s). Initiate it by clicking File>Import>Drill. Follow the same import settings as with the Gerber files. TIP: If we don’t import the Drill files, we won’t be able to extract the netlist(s) later on to export to PCB.
Select the Drill file(s) to load into the CAMtastic document. |
TIP: Select the appropriate import settings. |
Providing Information about the Layers

To extract the netlists, we need to first associate and establish the layer sets (for eg. the drill layer and top and bottom layers). Click on Tables>Layers Sets. You need at least ONE layers set to move on. You should also set the Layers Order by clicking Tables>Layers Order, otherwise, you will encounter an error when trying to export to PCB.
Insert a layer set by associating the drill layer(s) with the signal/plane layer(s). |
Extract the Netlists
We need to now extract the net(s) by clicking on Tools>Netlist>Extract. Now, the traces are identified with a net as they were during the PCB design process.
TIP: Ensure the netlist(s) are extracted from the Gerber files. You can export it to a PCB document. |
Export to PCB Document
To generate the PCB document, click on File>Export>Export to PCB (previously grayed out if the preceding steps are not performed). You will now see all the Gerber files being converted into the PCB document.
TIP: Select the desired trace(s) that you want to copy as a footprint. |
Open Gerber Files In Eagle
Copy as Footprint
After you have selected the trace(s) that you wish to copy, paste them in the Footprint PCB Library and create a new component for it.
Now you’re ready to rock-and-roll with your new footprint reference design! |
Summary
We have gone through a step-by-step analysis on how to import the reference design in Gerber files, extract the necessary layer and netlist information, convert them into the PCB document and thereafter be able to reuse it as a component footprint! Perhaps, if you had tried to draw this from scratch, you would have taken a full day to do just that.
I hope that you found my example useful and hope it will come in handy for any advanced users out there. Thanks for reading!
References
- https://techdocs.altium.com/display/ADOH/CAM+Editor+Reverse+Engineering+PCBs
- https://techdocs.altium.com/display/ADOH/CAM+Editor+Panels+for+Fabrication+and+Assembly
- http://techdocs.altium.com/display/ADOH/CAM+Editor+Data+Verification
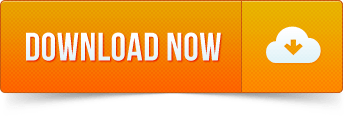